STAMPAGGIO ROTAZIONALE
Questa tecnologia, indicata principalmente per la costruzione di serbatoi, cisterne, contenitori chimici ecc. ovvero in tutte quelle applicazioni dove il contenimento di sostanze liquide e solide necessitano di un contenitore robusto, senza saldature, leggero e antishock, nasce negli Stati Uniti d’America alla fine degli anni ’30, ma la seconda guerra mondiale ne rallentò fortemente lo sviluppo che riprese poi negli anni ’50.
Si hanno però notizie di Stampaggio Rotazionale in Svizzera già a partire dal 1600 dove alcuni pasticcieri iniziarono a produrre uova di pasqua di cioccolato (e non… di plastica) utilizzando rudimentali clessidre.
Lo stampaggio rotazionale ebbe un lento sviluppo rispetto alle più nobili tecnologie di trasformazione plastiche quali l’iniezione, il soffiaggio e la termoformatura a causa delle bassa produttività rispetto ai costi d’esercizio.
Negli ultimi 5 anni lo sviluppo di questa tecnologia ha però subito un fortissimo incremento, quasi esponenziale, dovuto principalmente al miglioramento della progettazione impiantistica che ne ha drasticamente ridotto i costi, agevolandone la diffusione e il consenso del mercato; inoltre, la rientrata competitività economica, rispetto alle altre tecnologie plastiche, ha svelato il vero punto di forza di questo sistema produttivo: quello di ottenere prodotti privi di tensioni interne.
Lo stampaggio rotazionale consiste nel ricavare da uno stampo opportunamente costruito, manufatti plastici cavi, privi di saldature e tensioni, monoliti. Gli stampi utilizzati possono essere fabbricati in acciaio a lastre saldate opportunamente sagomate, o in alluminio per fusione di lavorazione CNC; devono essere cavi all’interno e possono essere composti anche da più parti, in modo da ottenere con estrema facilità sottosquadro, cosa fattibile ma estremamente difficile da eseguire con altre tecniche plastiche. Si possono ottenere, inoltre, prodotti con svariate tipologie di superfici, dalla lucidatura a specchio, alla goffratura pesante.
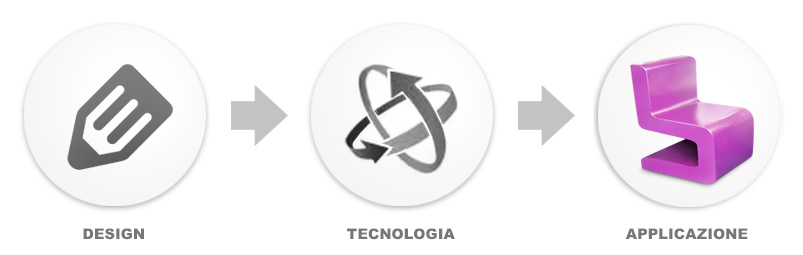
Gli stampi vengono montati su impianti specifici dotati di:
• Braccia rotanti su due assi, principale e secondario
• Camera forno
• Camera raffreddamento
Quando lo stampo è aperto viene versata la materia prima.
La materia prima si può trovare sotto forma di polvere (normalmente utilizzata) o liquida.
Le tipologie dei materiali usati sono molteplici:
• Polietilene lineare nelle svariate densità : LLDPE-MDPE-HDPE
• Polietilene reticolato : XLPE
• Poliamide nylon : PA
• Polipropilene : PA
• Etc…
Inoltre, la tecnologia permette di inserire con estrema facilità:
• Bussole aperte in materiali ferrosi di diversi diametri e filettature
• Flange in materiali ferrosi di diversi diametri
• Etc…
Chiudendo lo stampo contenente la materia prima e gli eventuali altri particolari elencati sopra, il ciclo produttivo ha inizio. Normalmente il ciclo è così composto:
• 20 minuti di permanenza nel forno
• Temperatura Forno circa 275 ÷ 310 °C
• 20 minuti di permanenza nella camera di raffreddamento, dove viene intervallata aria-acqua-aria
La materia prima in polvere contenuta nello stampo a contatto con il calore del forno si compatta cambiando il suo stato fisico da polvere a viscoso (simile alla viscosità del miele) ed unita all’azione rotativa del braccio che muove lo stampo con velocità molto blanda circa 12 ÷ 18 giri minuto, la distribuisce attorno alle pareti dello stampo stesso creando il vuoto all’interno. Successivamente avviene l’azione di solidificazione della materia prima nella camera raffreddamento. Per effetto del ritiro plastico della materia prima si ottiene il manufatto.